Zinc plating is one of the lowest cost, most effective options in electroplating for parts and components in a wide variety of industries. Also known as galvanization, zinc electroplating can be done quickly, effectively and with high levels of precision across any...
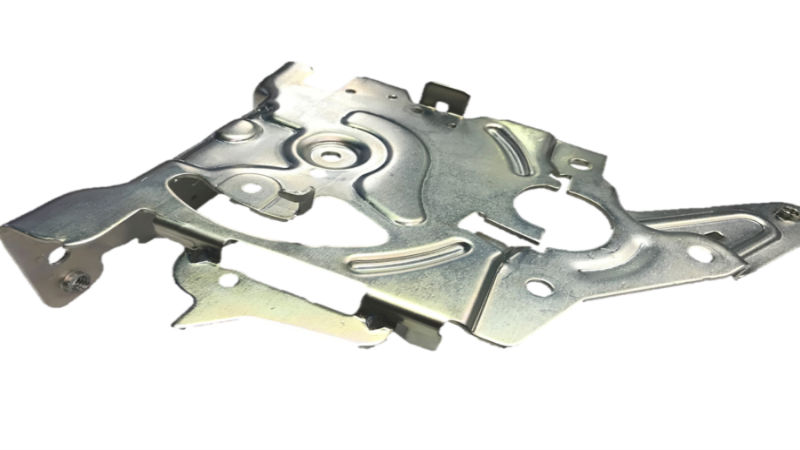